DI
Combustion Chamber Design
Large
Large slow running DI engines (under 1500 rpm) have 'open
chambers' where the piston has a very shallow dish shaped
with a bump in the middle. Air movement is minimal and the
multi hole injectors (often 8-12 hole) are set to inject a
fine mist into the dish. Due to the size of the combustion
chamber sufficient air is present to supply the fuel with
oxygen and the fuel combusts before it contacts surfaces of
the combustion chamber.
Small
With smaller higher speed engines it is not possible to produce
injectors with the multiple very small holes that would be
necessary to provide sufficient fuel distribution. The number
of holes is therefore reduced (3-5 hole). To achieve better
fuel/air mixing air turbulence is induced within the combustion
chamber.
Incoming air is set into rotation by the inlet valve being
positioned to one side of the cylinder head. The air rotates
around and down the cylinder as it is pulled in. This rotational
force is sometimes increased by having a helical induction
port passage where the air is guided into a semi-vortex swirl
around the valve stem on its way into the cylinder.
The piston has a bowl in its crown. As the piston approaches
the top of the cylinder the rotating air is forced into the
piston bowl. The rotational force is magnified by the reduced
diameter of the piston bowl. Thin, deep bowls have a higher
swirl rate.
At the same time air squish is initiated as the air is forced
from above the piston crown in towards the centre of the piston.
The squish forces meet at the centre of the cylinder and oppose
each other being forced downwards into the bowl where they
follow the bowl profile being led into a horizontal swirl.
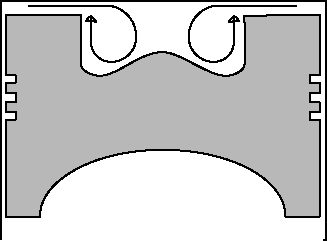
Simple bowl showing squish action - also described as torodial.
In order for the fuel and air to mix the fuel injection is
set to spray against the wall of the piston bowl. The drag
created by this contact stops the combusting fuel spray being
dragged with the swirl and allows the fuel to contact with
fresh oxygen. With thin bowls the spray does not have to penetrate
as far to reach the combustion chamber wall so a wider more
fine injection can be utilised that will mix more readily
with the fuel.
With the quickest engines large air movement is required
to give a fast mix. The fuel spray has to be more penetrating
to overcome the increased air forces and the injection event
rate is increased so that the fuel charge is swiftly delivered
and has longer to mix and combust.
A trick used by several engine manufacturers is to give the
bowl a lip to prevent the air squish motion pushing fuel above
the piston crown, so that the majority of the fuel charge
is mixed and burnt within the bowl. The lip also creates further
micro turbulence within the bowl. Engines with this re-entrant
lip design include VW/Audi tdi engines (thanks to John O for
this info), Perkins Prima, Perkins 42482 and some Isuzu square
(when looking from above) bowl chambers. The square chamber
produces micro turbulence from its rounded corners which provide
superior air-fuel mixing.
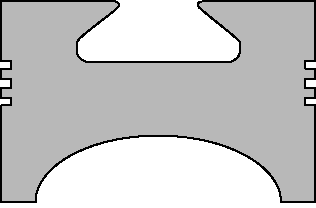
Perkins Squish Lip Re-Entrant Bowl Piston
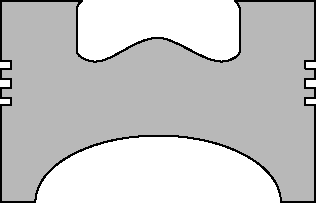
Isuzu Square Bowl Piston
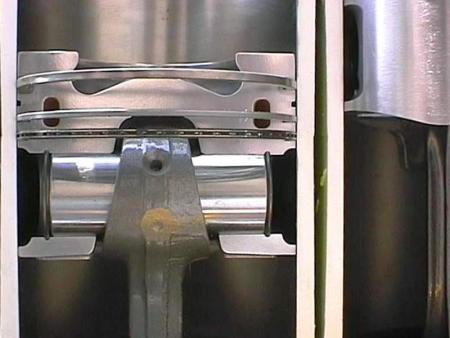
Chevy Duramax Piston (Cheers JMJ)
The Elsbett Piston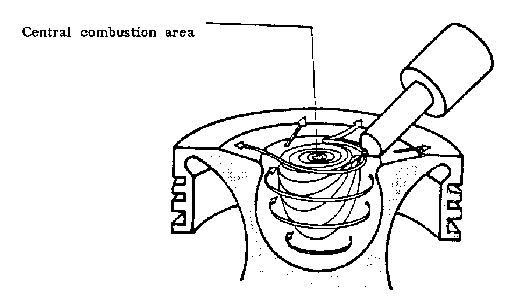
The Elsbett engine has a deep bowl which has a slight lip.
The main difference is that the fuel charged is injected in
such a manner as to 'blend perfectly with the air' and combust
within a central core of hot air, not contacting the chamber
walls, which is necessary for good air/fuel with other designs
examined.
The MAN M system (film) combustion chamber
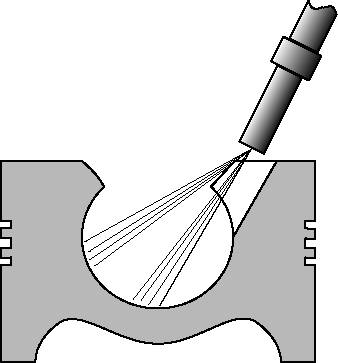
A similar shaped piston bowl to the Elsbett
system. With this design the fuel is injection is directed
onto the chamber wall where it spreads as a film, combusting
as the film evaporates due to the heat of the piston. The
heat of the piston has to be within a temperature range to
achieve fuel evaporation without causing thermal decomposition
and carburizing of the fuel.
Lessons to be learnt for Veg Oil
To summarise I would presume:-
Quick injection rate gives more time for the oil to begin
to combust.
Chamber shapes that create greater micro turbulence - the
Isuzu square chamber would appear superior in this respect
- should provide better fuel air mixing and faster combustion.
Deep re-entrant chambers should be more effective than shallow
chambers.
Comments, suggestions or observations will be gratefully
received from those with relevant experience or information.
http://biodiesel.infopop.net/2/OpenTopic?q=Y&a=tpc&s=465094322&f=166094322&m=7283049396&p=3
http://www.elsbett.com/gd/eteche.htm
http://www.elsbett.com/gd/etech.htm
http://www.univ-orleans.fr/ESEM/LME/Commun/Doc/pdf/21Resume1.pdf
'Advanced Engine Technology' by Heinz Heisler ISBN 0-340-56822-4
|