Engine
Suitability
Version 2.0 (20/4/2004)
Engine Suitability-Version
1.0
1 The Diesel Engine
2 Theory of Vegetable Oil Use as a
Fuel
3 Engine suitability
4 Heating the Oil
5 Biodiesel
6 Micro Emulsions and Blends
7 Vegetable Oil Engine Design
8 Vegetable Oil Furnaces and Heaters
9 Oil Types and Filtering
10 Taxation
11 Implications of Vegetable Oil
Fuel Use
12 Sources
Engine Suitability
There are many variations on diesel engine
design. Various design elements effect suitability for vegetable
oil fuel use.
Combustion Chamber
Direct Injection (DI)
Problems can occur with deposits building within
DI engines when running on vegetable oil. The design of the
combustion chamber and the injector along with their positioning
will affect suitability
The Elsbett DI multifuel engine [34] [35] produced
from the 1970s could be fuelled with vegetable oil or diesel.
This engine has a deep, almost spherical, combustion chamber
within the piston. The injector nozzle protrudes into the
cylinder and delivers fuel directly to the centre of the combustion
chamber. The unique design ensures that fuel is burnt without
contacting the combustion chamber walls.
Fuel oil with a substantially greater viscosity will cause
degraded atomisation from injectors that are deigned for a
thinner fuel. Combustion will be adversely affected causing
an increase in emissions and giving a greater potential for
harmful deposits on the injectors and within the combustion
chamber.
Hemmerlein et al.[28] tested three unmodified
DI engines, one 2.6 litre air cooled and two larger, 6.6 litre
and 12 litre, turbo charged and intercooled with liquid cooling,
running rapeseed oil. All three engines failed durability
tests due to problems caused by carbon build ups.
Karaosmanoglu et al.[30] tested a Panccar Motor
1 litre single cylinder DI engine running sunflower oil. The
engine successfully completed long-term engine testing when
it was started and shut down for 5 minutes with diesel fuel.
The engine was run at a constant low speed under partial load.
Both Pflanzenoeltechnik-Nord GmbH [49] and Albrecht Transporte
[50] report up to 250,000 km travelled using vegetable oil
in a number of different modern DI trucks.
DI engines with a re-entrant bowl type combustion chamber
- where the bowl has a lip around the top to encourage fuel
to stay within the combustion chamber, away from the cylinder
walls and piston rings – should have lower frequencies
of ring land fouling associated problems. The lip of a re-entrant
bowl also causes micro turbulence within the chamber, which
aids fuel/air mixing and thus gives superior combustion.
Deeper combustion chambers, which are generally
of a smaller diameter give rise to increased swirl which aids
atomisation and injection pressure can be set higher as the
fuel does not have to penetrate as far to reach the combustion
chamber walls (which allows wall wetting and proper combustion).
The increased squish area of this design gives a larger overall
surface area and a greater output of hydro carbons due to
heat loss.
Indirect Injection (IDI)
The fuel is injected as a jet and atomised
in a separate combustion chamber before it enters the cylinder
and completes combustion. The atomisation processes, caused
by high air speeds, within the annexed combustion chamber
after injection along with the remoteness of injection from
the piston rings make these units less prone to problems from
using thicker fuel oil.
Hemmerlin et al. [28] tested three unmodified
IDI engines running on rapeseed oil. A small 1.6 liter swirlchamber
engine failed durability testing due to carbon build up within
the engine. Two larger IDI engines, a 6.2 litre prechamber
engine and a 5.7 litre swirlchamber engine completed the durability
testing.
Fuls et al.[31] found that an unmodified Caterpillar
IDI engine in a tractor successfully completed extended service
tests using sunflower oil as a fuel. This test led to Caterpillar(South
Africa) providing a warranty on this engine running this fuel.
Togashi et al. [29] found that a small Yanmar IDI engine could
be reliably operated on refined or deacified rapeseed oil.
Niegsch [10] found a Mercedes prechamber engine
can be operated on refined, food grade rape oil for over 200,000
km with only minor problems.
Injector Pump (IP)
Mechanical Injection
In-Line Pump
These pumps have proved to be very reliable
when fuelled with vegetable oil fuels. Mercedes IDI engines
with in-line pumps have been run, without modification, fuelled
with rapeseed oil for extended periods.
Rotary Pumps
The single pumping mechanism which pumps fuel
to all cylinders has to work harder than its in-line equivalent.
On a four cylinder engine the pump mechanism is pumping four
times to every one pump of an in-line. The increased stress
on the pumping mechanism, of pumping more viscous fuel, is
multiplied.
Rotary pumps generally contain a sliding vane
type transfer pump to supply a constant excess of fuel at
pressure to the injector pump.
There are also two common designs of rotary pump mechanisms
Bosch Type: The entire rotating valve system moves backwards
and forwards pumping the fuel.
Lucas/CAV Type: Uses two plungers that are flung outwards
by the rotor, they are pushed inwards by a cam to expel the
fuel.
The Lucas/CAV units has been found to be susceptible to malfunctions
when running on vegetable oil, thought to be caused by their
less rugged construction and possible accumulation of dirt,
held by centrifugal force, within the plunger cylinders which
would be cleared by the backwards and forwards pumping motion
of the Bosch unit.
The Lucas/CAV units come with either metal or fibre vanes
in the transfer pump which pulls the fuel into the IP. Transfer
pumps have been damaged, examination of damaged pumps has
lead to the conclusion that the damaged was caused by the
increased heat created pulling thicker fuel or a swelling
of fibre vanes, metal vanes can be fitted to alleviate this
possible problem. Another possible cause of problems is expansion
or contraction caused by fuel of a radically different temperature
suddenly being introduced. Great care should be taken when
using this type of pump. The fuel should be filtered very
thoroughly and vegetable oil heated carefully.
If an engine is to be started with cold (thick) oils it
is advisable to keep the engine speed low until the oil has
been heated to reduce stresses on the pumps, this is especially
the case with rotary pumps.
Injector pumps have been modified to allow them to function
more reliably with vegetable oil. Lucas/CAV rotary pumps can
have fibre vanes up rated. The main pumping mechanism(s) within
an IP can be modified by the use of lapping paste on the pump
plunger(s) so that it requires a similar force to move when
pumping SVO as when using diesel or channels can be cut into
the rotor in a rotary pump to increase lubrication and reduce
heat. This will reduce stresses on the pump but in many cases
may be unnecessary. Injector pumps are very precise systems
and modifications should only be undertaken by a suitably
experienced engineer.
Electronic Injection
The more precise injection controls and higher injection
pressures of new electronically controlled systems are capable
of providing superior combustion. However equipment may need
tuning to run vegetable oil fuels. Injection events are governed
by computers, which monitor a number of different factors
to give the best combustion performance. The properties of
vegetable oil based fuels have the potential to confuse the
computer as the fuel may have properties that may be outside
the parameters expected by the computer or under a given injection
program the fuel may behave differently to how the computer
expects and not combust effectively. Damage to sensing equipment
is also possible.
Owen [36] reported a damaged incremental angle sensor within
a Bosch VP44 injector pump fitted to an Vauxhall Astra Diesel
Tdi while running 80% recycled used vegetable oil, 10% industrial
methylated spirits (denatured ethanol), 5% butanol and 5%
petrol mix.
Cummins [37] reported, “There are confirmed accounts
of ISB engine fuel pump failures due to the effects of alcohol
induced de-lamination of an internal timing sensor component.
Robert Bosch, the fuel pump manufacturer prohibits alcohol
blended fuel in the VP44 fuel pump on the ISB/QSB Cummins
engine."
Frei [38] described modifications to a Mercedes Sprinter
CDI (common rail). The engine would not start on vegetable
oil when the engine was warm. The engine control computer
monitors engine temperature when starting. Injection quantity
is reduced when starting with a warm engine. The computer
had to be tricked to think that the engine was cold starting
so that it increased the fuelling and enabled initial combustion.
Burton[51] reported that Elsbett engineer Alexander Noack
from Elsbett used a laptop to reprogram the onboard computer
so that it would think that the engine is cooler than it is
and heat the glow plugs for a longer duration – allowing
for smooth starts with vegetable oil.
Injectors
Pilot Injection
Injection systems are increasingly being designed with a
pilot injection. A small quantity of fuel is introduced before
the main fuel load is injected. Ignition of this fuel commences
and ‘conditions’ the combustion chamber, providing
heat that reduces the ignition delay of the main fuel load.
Some electronically controlled injection systems provide
the pilot fuel as a separate injection. High-speed fuel delivery
control solenoids allow multiple injections of fuel during
the fuel delivery phase. The ferocity of the main combustion
event is reduced as less fuel is delivered during the now
reduced ignition lag period of the main fuel load.
Fuel introduced during the ignition delay or lag period,
which is the time between fuel being introduced to the combustion
chamber and conditions becoming correct for ignition to commence,
combusts quickly, the larger the amount of fuel present at
the onset of ignition the greater the noise.Ignition lag is
increased with cold engines and at low engine loads, as less
heat is available within the engine and combustion begins
later. The fuel properties and quality of atomisation also
effect ignition lag. Ignition lag is the cause of ‘diesel
knock’ or ‘clatter’.
Injectors with a pilot injection function were introduced
to reduce engine noise by reducing the amount of fuel injected
during the ignition lag period.
Experiments using a shock tube at high temperature and increased
pressure found sprays of vegetable oil fuels burnt in a different
manner to diesel, where the flame was reasonably uniform.
Vegetable oil fuels produced pockets of burning, some of which
continued for longer than would be available in an engine.
It was thought that these were larger fuel droplets. These
part burnt droplets would cause engine deposits. A second
injection of fuel into high temperature and pressure conditions
was found to rapidly combust in a uniform manner over the
entire reaction volume. [2]
These experiments would suggest that pre injection systems
should help to enable vegetable oil fuels to combust more
completely.
DI engines sometimes utilize two spring nozzle holders to
give a pre injection. The valve is held shut by two springs.
The increasing fuel pressure overcomes the first spring, which
allows a small quantity of fuel to be injected. As the fuel
pressure increases it overcomes the pressure of the second
spring and the main injection event begins.
IDI engines use a number of different pintle nozzles designs
to achieve a pilot injection effect.
Delay or Throttle Pintle
As the needle lifts from its seat the longer throttle pintle
still largely blocks the injection orifice allowing a small
amount of fuel to be injected. As injection continues the
throttling pintle clears the injection orifice allowing the
main fuel charge to be delivered. Sometimes the throttling
pintle is slightly tapered to provide a gradually increasing
injection rate until the main injection takes place towards
the end of the needle lift. [39,41]
Standard Pintle Nozzle
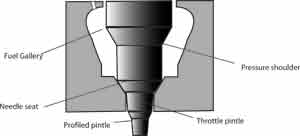
Throttle/Delay Pintle Nozzle
Hole Type Pintle
With this throttle pintle design, as the needle begins to
lift, the fuel is able to flow into small bores that provide
a pilot injection from a spray hole in the centre of the pintle.
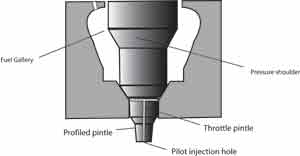
Pintaux Pintle Nozzle
The Pintaux nozzles are similar to hole type except the
pilot injection bore is in the nozzle body rather than the
needle. The fuel jet is aimed at the throat from the engine
cylinder to the prechamber. This aids starting as at low needle
lift conditions (such as when the engine is being started)
the main fuel charge is directed at the hot air rushing into
the prechamber where combustion is most likely to occur.
Flat-Cut Pintle
This is a throttling pintle with an additional flat cut
to allow a greater volume of fuel to flow at low levels of
needle lift. As with the hole type pintle the gap between
the throttling pintle and injection orifice is very small
and during the pilot injection phase most fuel flows through
the flat cut area
Industrial and marine engines are available equipped to burn
heavy fuel oils. Injectors fitted to these engines are designed
to provide good atomisation and avoid coking with these thicker
fuels.
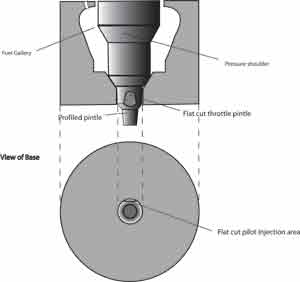
Anti-Coking Nozzle Designs
Flat-cut pintle nozzles have been found to be far less prone
to coking due to the increased flow volume within the flat-cut
area that stops deposits forming. [39]
Seat hole or valve covered orifice (VCO) injectors are multi
hole injectors in which the start of the spray hole is located
within the valve seat. With the traditional multi hole injector
design the fuel left downstream of the valve, in the sac and
nozzle holes, is heated by combustion and some fuel enters
the combustion chamber late within the combustion event. This
fuel only partially combusts and causes associated hydrocarbon
emission problems and deposits on and within the nozzles.
VCO injectors help to negate these problems by significantly
reducing the amount of fuel that can leave the injector after
the injection event and by blocking the flow of combustion
products into the injector sac [39,40,41]
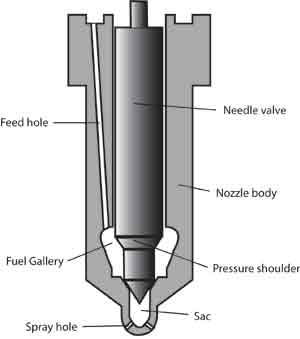
Multi hole nozzle
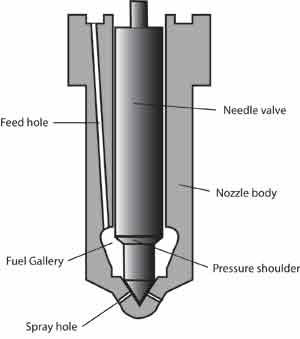
VCO Nozzle
Non VCO injectors are available with a reduced sac capacity
that perform somewhere between standard multi hole and VCO
injectors. Conical sac hole injectors are available which
have a reduced sac volume compared to standard cylindrical
sac injectors. Also injector needles are used with an extension
from the tip to decreases sac volume with the valve closed.
Needle motion sensor, optical ignition sensors, injection
lag, ignition lag and vegetable oil fuels.
NOx emissions have been found to increase with vegetable
oil fuels, it has been suggested that this is due to the larger
molecules found in these fuels which are less compressible
and would lead to a reduced injection lag, that is the time
between fuel being pumped by the IP and being delivered by
the injector nozzle. Advancing the time of combustion is known
to increase combustion pressures and temperatures, which leads
to higher NOx levels. Injectors fitted with needle motion
sensors detect the exact time of fuel delivery and the pump
timing is modified to compensate [39][52].
Toyota introduced an optical ignition sensor that enables
the ignition delay to be observed. The control unit can optimise
the timing to compensate for differing fuels and engine wear
[42].
Glow Plugs
Some vehicles glow plugs have an after glow function where
the glow plugs stay on after starting for a few minutes to
smooth cold running. This function improves poor combustion
within a cold engine.
Upgrade kits are available for some vehicles from both Bosch
and Buru. The replacement plugs are of a heavy-duty construction
to withstand the extended heating times. Buru after-glow plugs
are marked GN for Nachglueh (post-glow) compared to GV for
Vorglueh (pre-glow). Bosch produce Duraterm glow plugs which
are designed for use with afterglow systems. The later Duraterm
Chromium are of a more rugged design.
1 The Diesel Engine
2 Theory of Vegetable Oil Use as a
Fuel
3 Engine suitability
4 Heating the Oil
5 Biodiesel
6 Micro Emulsions and Blends
7 Vegetable Oil Engine Design
8 Vegetable Oil Furnaces and Heaters
9 Oil Types and Filtering
10 Taxation
11 Implications of Vegetable Oil
Fuel Use
12 Sources
|